Луч, вакуум, «лебедь»
Маёвец участвовал в восстановлении уникальной технологии.
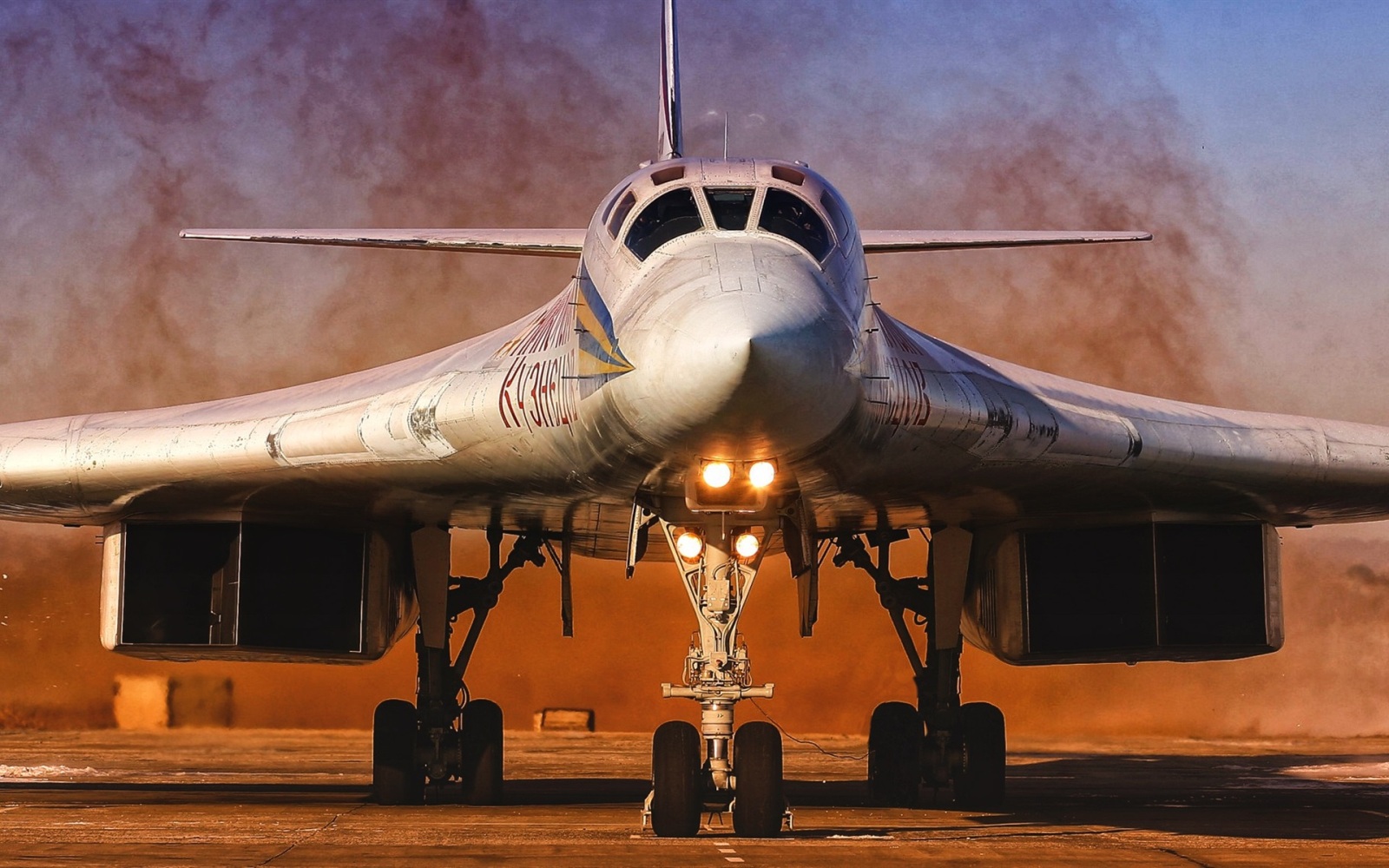
В Казани на авиационном заводе им. С.П. Горбунова вновь проводится электронно-лучевая сварка титановых деталей. Уникальная установка для этого процесса была создана еще в 80-х годах. Однако в лихие 90-е она стала «ненужной». Теперь оборудование, стоявшее без дела почти 30 лет, модернизировано и вновь используется. В возрождении этой компетенции деятельное участие принял выпускник МАИ, а ныне директор дирекции по технологии компании «Туполев» Сергей Тепаев.
Титан среди металлов
Его называют «космический металл». Однако без него сегодня никак не обойтись не только в космонавтике, но и в авиастроении, судостроении, автомобилестроении и всевозможных иных «строениях», а также в химической, оборонной, медицинской и других промышленностях.
Этот химический элемент открывали трижды независимо друг от друга англичанин, немец и француз. Сначала Уильям Грегор из города Крид в графстве Корнуолл в 1791 году выделил новый оксид неизвестного доселе металла, который назвал менакеновой землей. Четыре года спустя Мартин Клапрот из Берлинской артиллерийской академии в минерале рутиле открыл новый элемент. Клапрот уже давал названия новым химическим элементам в честь персонажей древнегреческой мифологии: в 1789 году он нарек полученное им черное металло-подобное вещество ураном (да-да, это тот самый уран, используемый ныне в атомной промышленности и боеголовках). Еще через десятилетие профессор Луи Никола Воклен из парижского Коллеж де Франс обнаружил тот же элемент в анатазе и понял, что это тот же самый оксид, что и в рутиле.
В итоге за элементом сохранилось немецкое название— титан. А вот из-за высочайшей химической активности и сложности очистки чистый титан удалось получить лишь в 1925 году путем термического разложения паров иодида титана. И лишь в 1940 году люксембургский металлург Уильям Кролл получил первые несколько десятков килограммов чистого металлического титана магниетермическим методом. Этот способ используется в промышленности до сих пор.
Благодаря целому ряду достоинств титан сразу привлек внимание конструкторов и материаловедов. Он в два раза легче железа, пластичный, ковкий, хорошо обрабатывается, достаточно твердый, долговечный и не теряет этих свойств при высоких температурах (до 400 °C). К тому же титан не разрушается со временем ни на воздухе, ни в речной, ни в морской воде, стоек в любых агрессивных средах.
Возрождение «Белого лебедя»
Знакомьтесь: Сергей Тепаев. В 2010 году окончил первый факультет МАИ по специальности «Самолето- и вертолетостроение». Еще будучи студентом, в 2008 году Сергей пришел в компанию «Туполев» на должность инженера-технолога.
«В МАИ, по крайней мере на кафедре, где обучался я, тебя с четвертого курса считают уже инженером, относятся и ставятся задачи как будущему специалисту авиационной отрасли,— вспоминает Сергей.— Один из преподавателей как-то сказал, что, помимо технической базы, которую вы получаете в процессе обучения, вас обучают еще и умению общаться с людьми, умению прислушиваться и слышать. В работе коллектива, по моему мнению, умение слышать специалистов — самое главное».
Маевская методика оправдала себя на 100%: в 2012 году Тепаев уже возглавлял технологическую службу ЦКБ, занимающуюся технологическим сопровождением самолета на всех этапах его жизненного цикла.
Знакомьтесь: Ту-160, прозванный российскими летчиками «Белый лебедь». Это самый крупный в мире стратегический ракетоносец. Первый полет совершил в декабре 1981 года. Самолет известен среди прочего еще и тем, что при его строительстве используется наибольшая доля титана — 26–28% от общего веса.
В 2016 году Минобороны России приняло решение начать закупки новых Ту-160. Для этого требовалось восстановить производство «лебедя», который собирали на Казанском авиационном заводе им. С.П. Горбунова (сейчас это один из филиалов компании «Туполев»).
Один из важнейших элементов конструкции Ту-160 — центральная балка, изготовленная из титанового сплава ВТ6ч, массой около 6 т. Балка — наиболее нагруженный элемент конструкции Ту-160: к ней крепятся основные механизмы, обеспечивающие изменение стреловидности крыльев, отъемные части крыла, узлы навески шасси. Балка собирается из нескольких частей большой толщины из титановых сплавов. Чтобы минимизировать массу балки, для соединения ее частей решили использовать сварку. Получилось около 180 м сварных швов. Тип сварки выбрали на основе электронно-лучевой технологии.
«Сама эта технология всемирно известна,— рассказывает Сергей Тепаев.— Еще в 1950-х годах немецкий физик Карл-Хайнц Штайгервальд продемонстрировал использование электронного луча для получения отверстий и прецизионной обработки. В 1957 году француз Жак-Андрэ Стор создал первую в мире электронно-лучевую установку для сварки. Но уже на следующий год та же технология была впервые применена в СССР при совместном участии МВТУ и МЭИ. В 1980-х годах технологию сварки электронным лучом начали широко применять в промышленности, в том числе и авиационной— при изготовлении элементов из титановых сплавов для Ту-160».
Участок электронно-лучевой сварки на заводе в Казани включает в себя две уникальные установки: непосредственно электронно-лучевую установку ЭЛУ 24×16, предназначенную для проведения процессов сварки лучом в вакууме, и печь вакуумного отжига УВН 45-180/8,5, при помощи которой снимается остаточное напряжение после сварного процесса. «Уникальность участка электронно-лучевой сварки на Казанском авиазаводе заключается в габаритных размерах установок самой сварки и печи— их объем 1350 м³ и 850 м³ соответственно,— говорит Тепаев.— Это одна из самых крупных в мире подобных установок».
Модернизация с «Техническим азартом»
Для возрождения технологии электронно-лучевой сварки на Казанском авиазаводе в 2016 году были образованы рабочие группы из специалистов-технологов «Туполева», а также из Всероссийского научно-исследовательского института авиационных материалов (ВИАМ) и компании «Электромеханика» и НИТИ «Прогресс». В их состав входил и Сергей Тепаев, назначенный к тому моменту на должность директора дирекции по технологии «Туполева». Роль фирмы «Туполева» заключалась прежде всего в организации и координации работ по восстановлению участка, увязке технических заданий на модернизацию оборудования и отработку технологии изготовления в целом. «Участок электронно-лучевой сварки является для проекта по восстановлению производства самолета Ту-160 одним из ключевых,— делится Тепаев.— Для меня участие в восстановлении ЭЛУ явилось прежде всего примером слаженной работы коллективов различных предприятий: «Туполева», «Электромеханики», НИТИ «Прогресс», ВИАМа. Все специалисты работали с «техническим азартом», испытывая гордость от того, что удается внести и свой вклад в столь масштабный и уникальный проект».
Процесс изготовления балки проходит в несколько этапов. Готовятся сборки балки, каждая или несколько сборок помещаются в камеру, откачивается глубокий вакуум до 10–4 мм рт. ст. При помощи электронной пушки (на ЭЛУ их две), установленной на роботе-манипуляторе, выполняется сварка. Далее оценивается качество шва (визуально и средствами неразрушающего контроля). При этом скорость сварки может достигать 36 м/ч.
Затем готовый агрегат перегружается в печь вакуумного отжига. Она — крупнейшая в отечественном авиастроении: длина рабочей зоны — более 20 м, длина установки — более 60 м. Печь обеспечивает равномерный нагрев со скоростью от 20 до 200 °C/ч. Здесь балку нагревают до 750 °C для снятия остаточного напряжения.
При восстановлении производства установку электро-лучевой сварки модернизировали. Обновлена система управления. Теперь используются две сварочные пушки вместо одной раньше. На установке смонтировали более надежную и эффективную вакуумную систему. За счет энергосберегающих технологий сократился расход электричества.
Марк Полов